Syringe Pump Troubleshooting
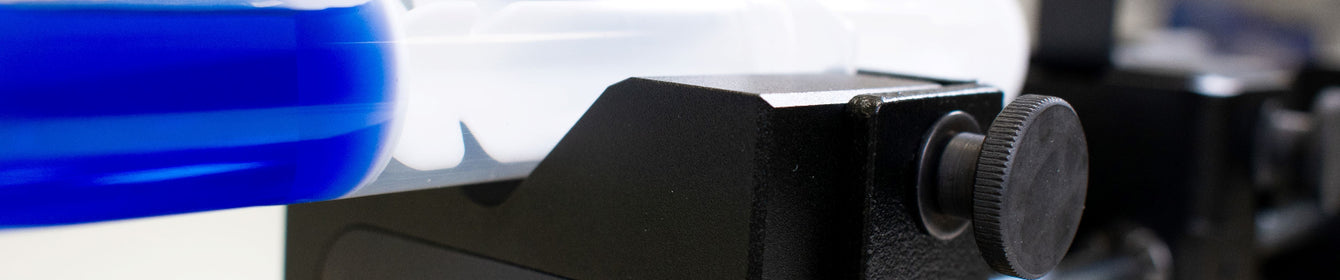
How to Prevent Solution Dripping After the Syringe Pump has Stopped
When you are auto dispensing solvents, droplets are sometimes dispensed after the syringe pump has stopped. The cause of this dripping can be due to several factors. These include which syringe type you use, the presence of air bubbles, and the viscosity, density, and surface tension of your solution.
Drips most commonly occur after the solution has been dispensed where there is a pressure difference between the inside and outside of the syringe. This can happen when air bubbles get trapped inside the solution, resulting in a compression of the gasses during dispense. After the pump has stopped, the compressed air expands and pushes solution out of the syringe.
Plastic syringes and tubing can also become elastically deformed over time, a process which will allow drips to form.
You can take several steps to avoid dripping. These include removing bubbles from the syringe before you load it, using tubing and syringes that show limited amounts of elastic deformation, and reducing the overall pressures in the syringe. To avoid a build-up in the syringe, consider using a lower dispense rate, reducing the viscosity of solution, or reducing the velocity of the solution by using pipes and needles with a wider diameter.
Sometimes, dripping occurs when you use a dense solution with a low surface tension and viscosity. Here, the adhesive forces between the surface of the needle, the tubing, and the molecules in the solution are often lower than the gravitational force acting upon the solution inside the tube. This results in a continuous drip, only stopping when the gravitational force acting on the solution becomes lower than the combined adhesive forces of the solution and the increasing pressure difference (due to displaced volume).
To reduce the effects of dripping from dense, low surface tension solutions, use tubing and needles with a lower diameter. Alternatively, try tilting the tubing and needle horizontally to reduce the gravitational force being exerted in the direction of the tubing.
Error codes 0x0E1 and 0x0E2
The syringe pump has two sets of switches at the end of travel. The first switches in each pair are software limiting switches which are designed to stop the motion of the syringe when pressed. If the software switch has failed to trigger and stop the motion of the pump, a secondary hardware switch is designed to cut the power to the motor and display the 0x0E error code.
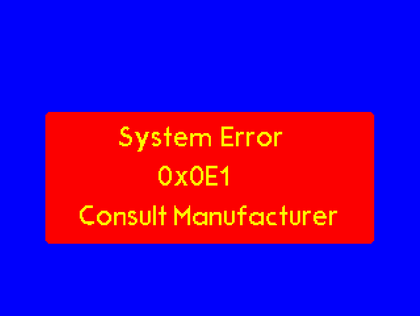
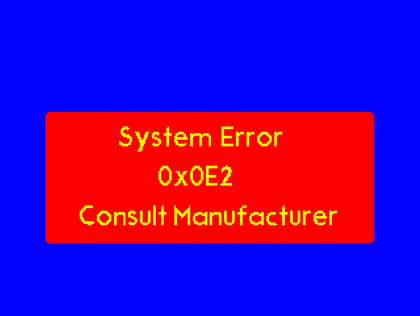
The 0x0E1 code indicates that the set of switches closest to the motor have been triggered. The 0x0E2 code indicates the set at the syringe end have been triggered. To fix the error, rotate the lead screw so the pump moves away from the switch sets and then restart the system.
Inconsistent Flow Through the Syringe Pump
Syringe pumps can be very helpful when you need a uniform flow of material. You can use them in combination with other coating techniques such as spin coating, bar blading, or slot die coating (our slot die coater has a syringe pump built-in). However, as with any coating technique, creating uniform thin films with a syringe pump sometimes requires some trial and error.
First, it is important to ensure that the flow rate is optimised for each new solution. Factors such as solution viscosity, cohesion and solvent volatility will determine how smoothly the material flows through and from the syringe. If the solution is too viscous, you might consider diluting the solution with more solvent.
Additionally, dust or contamination within your solution will interrupt smooth fluid movement and may block the syringe. This can also be a problem if your solution is prone to aggregating. Likewise, bubbles in your solution will lead to an interrupted outflow through the connected tube, possibly ruining your deposition or experiment. We recommend that whenever possible, you should filter solutions before use. Also, you should always use a fresh or clean syringe when using one of our syringe pumps.
How to Reduce Back Pressure
Solutions with high viscosity or concentration may flow turbulently or get stuck in deposition tubes that are either thin, or particularly long. This will put back pressure on the fluid all the way up the tube to the syringe pump, which can cause the movement to jam. This is more likely to happen if you try and deposit viscous solutions at high deposition rates.
When using viscous solutions in any syringe pump, try to use as short a tube as you can to reduce chances for blockages to form. If blockages are still an issue, you may need to use a tube with a thicker diameter. Additionally, when optimising deposition of a viscous solution, start with a slow deposition speed and work up.
Syringe Pump
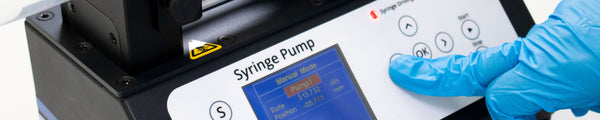
Contributing Authors
Written by
Product Developer
Application Scientist