Thin Film Solar Cells: Second Generation Solar Cell Technologies
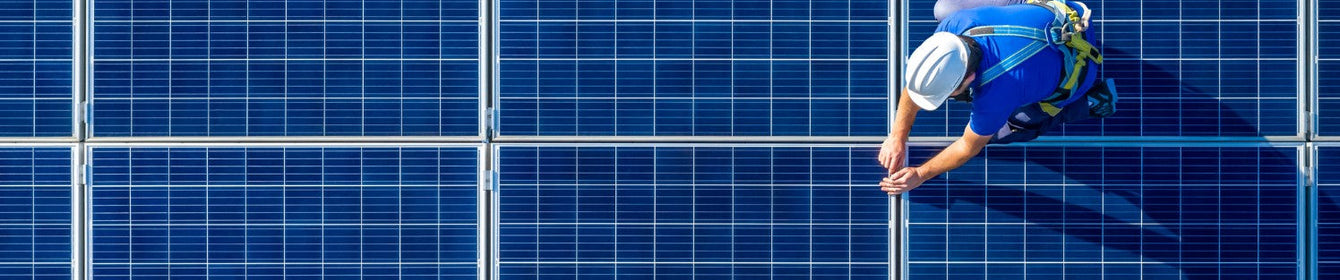
Second-generation solar cells are often referred to as thin film solar cells due to their construction. Instead of using thick silicon wafers, these cells use layers of semiconductor materials that are only a few micrometers thick. This thin structure reduces material costs and allows for more flexible applications.
Due to their high efficiency and well-established manufacture, first-generation crystalline silicon (c-Si) solar cells currently dominate the solar cell market. However, c-Si is expensive, and the cells have a long payback time, meaning that initial costs must be reduced for solar to become more fully adopted. This is one of the main motivations for using thin-film solar cells,1 where the active layer of photovoltaic material is much thinner than with c-Si (typically in the range of nanometres up to micrometres). Thin active layers reduce manufacturing and module cost, allowing more straightforward production. They open up the potential for flexible and semi-transparent solar cells.
Solar Beyond Silicon: What are the generations of solar cell?
Solar technologies beyond silicon are often categorised into ‘generations’, based on how advanced they are. Crystalline silicon solar cells fall into the ‘first generation’. Record efficiencies for other technologies can be seen in the figure below.
Second-generation cells are thin-film technologies that are often commercially available, such as:
- Copper indium gallium selenide (CIGS) - flexible metal blend with highest efficiencies
- Cadmium telluride (CdTe) - low production costs
- Gallium arsenide (GaAs)
- Amorphous silicon (a-Si:H) - requires less silicon than 1st gen solar cells
These cells are typically more cost-effective and use less material, though they are generally less efficient than first-generation cells.
Third-generation cells are less commercially-advanced ‘emerging’ technologies. This includes organic photovoltaics (OPVs), copper zinc tin sulphide (CZTS), perovskite solar cells, dye-sensitised solar cells (DSSCs), and quantum dot solar cells. The current article compares OPVs to second-generation thin-film solar technologies.
What Matters When Comparing Solar Cell Technologies?
Solar cell technologies are primarily compared by their achieved 'power conversion efficiency' (PCE, or just ‘efficiency’). High efficiencies are important as they will allow for lower system cost. This is because they use less active area, due to the area-dependent balance-of-system costs (such as wiring, mounting and hardware.)2 The cost and weight of the material itself are also important, but the active layer of a cell typically contributes to only <50% of the costs of the full photovoltaic system3 - so this must be balanced with efficiency.
The fundamental factors limiting this efficiency (e.g. high rate of recombination or a non-ideal bandgap) are also important, as certain factors are easier to control and overcome compared to others. The record efficiencies of materials can be compared to the Shockley-Queisser efficiency (SQ) limit4 for their specific bandgap (shown in the figure below), which illustrates the maximum possible efficiency.
Beyond simple efficiency obtained, there are other important factors to consider - such as the susceptibility of the cell's performance to external conditions. Different types of solar cells have different defect tolerances and dependencies on:
- Incident power3
- Temperature
- Angle of incident light
Scalability is also vital. This will be influenced by the abundance and toxicity of materials, along with the material's stability and ease of manufacture. For example, solution-processable layers will allow fast and cheap roll-to-roll production. Materials with poorer stability require more effective and expensive encapsulation,2 which will contribute to overall costs. However, degradation pathways may vary across different technologies, and may therefore be easier to tackle for some compared to others.
Lastly, the environmental impact of the technology across its life cycle is also significant. The emissions generated by the production of a solar cell (with contributions including extracting the material, processing the active layer, and manufacture of modules) can be summarised using the term ‘greenhouse gas emissions’ (GHG) or ‘global warming potential’, typically given in g CO2-eq/kWh.5
Materials with high GHG in production reduce the effectiveness of solar at decreasing emissions, and are thus less environmentally favourable. Similarly, energy of manufacture can be summarised by energy payback time (EPBT), which is defined as the time (typically in years) the solar cell will take to generate as much energy as was consumed during its production. The disposal and recycling potential of a material will also contribute to its environmental impact.
Organic Photovoltaics Compared to 2nd Generation Solar Cells
Copper Indium Gallium Selenide (CIGS)
CIGS cells have achieved the highest efficiency for a true thin-film solar cell. At 22.6%,6 they are comparable to commercial crystalline silicon, and far exceed the current efficiencies of OPVs. An advantage they share with OPVs over other second-generation cells is that they allow the band gap of the semiconductor to be tuned. In this case, by varying the In:Ga and Se:S ratios to obtain around 1.0 to 2.4eV,3 allowing targeting of an ideal band gap and applications in tandem solar cells.
However, CIGS are expensive (due to the rarity of indium), and manufacture can be difficult. The complex stoichiometry and multiple phases means that it is a challenging process to optimise CIGS cells,2 and this may restrict large-scale production in the future. The main advantages of OPVs compared to these are low-cost materials, and easy manufacture and optimisation.
Cadmium Telluride (CdTe)
At 22.1%,6 CdTe has achieved similar efficiencies to CIGS. It also has a band gap close to ideal at 1.43eV,3 with advantages including good absorption and low energy losses. CdTe solar cells can be made through low-temperature processes, allowing flexible and affordable production (as with OPVs) - which is preferable to expensive and time-consuming high-temperature processes. CdTe currently has the largest market share of all thin-film technologies.3
However, cadmium is toxic, and tellurium is particularly rare (being 300,000,000 times less abundant than silicon).2 These factors may point to potential issues with long-term, large-scale production in future. However, there has been some introduction of CdTe PV recycling by manufacturers.1 In terms of component toxicity and natural abundance, OPVs are advantageous compared to CdTe.
Amorphous Silicon (a-Si:H)
In comparison to conventional wafer-based c-silicon, hydrogenated amorphous silicon (a-Si:H) uses a randomly-organised structure. It yields a higher band gap of 1.7eV, in comparison to that of 1.1eV for c-Si. This allows stronger absorption in the visible region of the spectrum,1 albeit less well-matched to the infrared. Stronger absorption facilitates thin-films of silicon (in the region of 300nm)2 allowing for cells that have a lighter weight than c-Si, and with the potential for flexibility. Silicon also has little issues with abundance, but amorphous silicon has been limited in adoption due to low efficiencies (with a record of 14.0%)6 and potential photo-induced degradation issues.2 Low efficiencies and stability issues are features it shares with OPVs. However, over the course of production, amorphous silicon has significantly higher greenhouse gas emissions and energy payback time (as can be seen in the figure below).
Gallium Arsenide (GaAs)
GaAs solar cells have achieved the highest performance of all single-junction solar cells, with a record of 28.8%6 and a near-optimum bandgap of 1.42eV. GaAs cells use thin films of active material, and hence are technically thin-film cells - but this is typically deposited onto a GaAs wafer and then separated, with the wafer reused. This means some of the disadvantages of wafer-based c-Si apply - namely, expensive and difficult manufacture due to the requirements for high material purity. GaAs is mostly used for high-efficiency applications where cost is not a limiting factor (e.g. solar cells in satellite applications). As such, it fills a different market niche to OPVs, which have significantly lower efficiencies but maintain far cheaper and more straightforward manufacturing.
Summary
As illustrated in the record efficiency graph, OPVs have achieved significantly lower efficiencies than the second-generation solar cells discussed here. This is mostly due to the differences in ease of exciton dissociation between inorganic and organic semiconductors, and the high rates of non-radiative recombination in OPVs.3 Long-term photo and thermal stability is also better for most of the second-generation solar cells compared to OPVs. However, OPVs have easier manufacture and higher defect tolerance than many inorganic materials.2 They also have a particularly low EBPT7 and GHG5 values, and few rare or toxic components. The tunability of OPVs is also important, as most second-generation technologies (apart from CIGS) have a fixed bandgap, which limits tandem applications.
Efficiencies continue to grow, and the manufacture and cost of OPVs is preferable to most inorganic semiconductor-based cells. Regardless, it remains to be seen whether performance will rise to a point where OPVs can compete with established second-generation technologies on a large scale.
Solar Cell Testing Kit
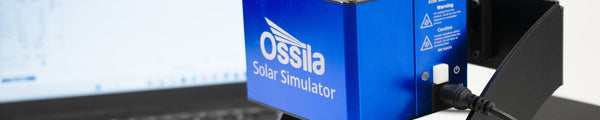
Learn More

Organic solar cells, also known as photovoltaics (OPVs), have become widely recognized for their many promising qualities. This page introduces the topic of OPVs, how they work and their development.
Read more...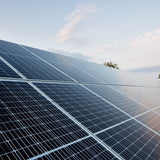
A solar cell is a device that converts light into electricity via the ‘photovoltaic effect’. They are also commonly called ‘photovoltaic cells’ after this phenomenon, and also to differentiate them from solar thermal devices. The photovoltaic effect is a process that occurs in some semiconducting materials, such as silicon.
Read more...References
- El Chaar, L., Lamont, L. A. & El Zein, N. Review of photovoltaic technologies. Renew. Sustain. Energy Rev. 15, 2165–2175 (2011).
- Jean, J., Brown, P. R., Jaffe, R. L., Buonassisi, T. & Bulović, V. Pathways for solar photovoltaics. Energy Environ. Sci. 8, 1200–1219 (2015).
- Polman, A., Knight, M., Garnett, E. C., Ehrler, B. & Sinke, W. C. Photovoltaic materials: Present efficiencies and future challenges. Science, 352 (2016).