Upgrading the Ossila Slot Die Coater
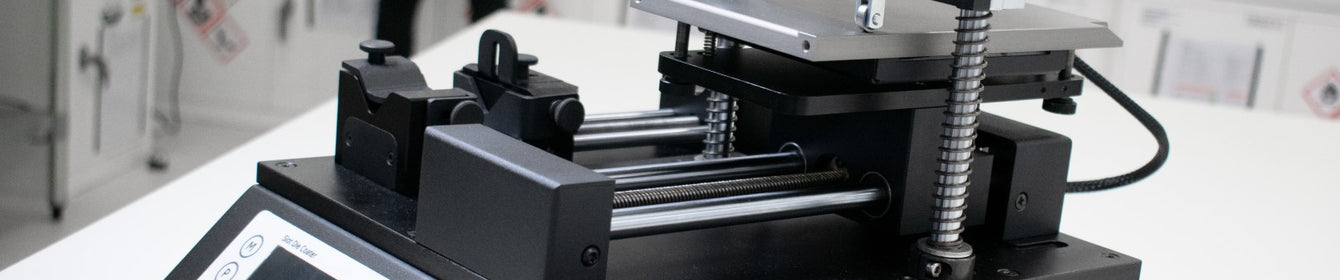
Slot die coaters are high-precision coating systems designed to apply a uniform thin films to over larger areas. This technology is widely used in industries such as electronics, photovoltaics, pharmaceuticals, and packaging due to its accuracy, repeatability, and scalability.
The Ossila Slot Die Coater is a complete slot die system, with an integrated syringe pump for synchronized start and end times. Here, we go through some of the improvements we have made to the Slot Die Coater to enhance user experience.
Improvement | Slot Die Coater Plus (Version 2) | Original Slot Die Coater (Version 1) | Advantage |
---|---|---|---|
Increased maximum hotplate temperature | 140 °C | 120 °C | Enhanced material compatibility |
Larger stage travel length | 150 mm | 100 mm | Improved productivity and versatility |
Increased slot-die coating width | 100 mm | 50 mm | Improved productivity and versatility |
Improved stage leveling mechanism | Two point stage | Three point stage | Enhanced coating quality and increased efficiency |
Bidirectional movement | Forward and reverse movement | One direction only | Expanded application potential |
Additionally, we plan on introduing these customizable add-ons very soon:
- Added foils for smoother coating
- Added meniscus camera for real time monitoring and adjustment
Increased Hotplate Temperature
One of the key improvements is the increased maximum hotplate temperature. This enhancement offers greater flexibility and efficiency in various coating processes. The previous maximum temperature was 120 °C, this has now been increased to 140 °C.
This higher temperature range allows for:
- Using materials that require higher curing or drying temperatures, expanding the variety of coatings that can be processed.
- Improved coating quality; higher temperatures can improve the flow and levelling properties of certain coatings, leading to smoother and more uniform films.
- Accelerated drying and curing times, improving throughput and efficiency in production.
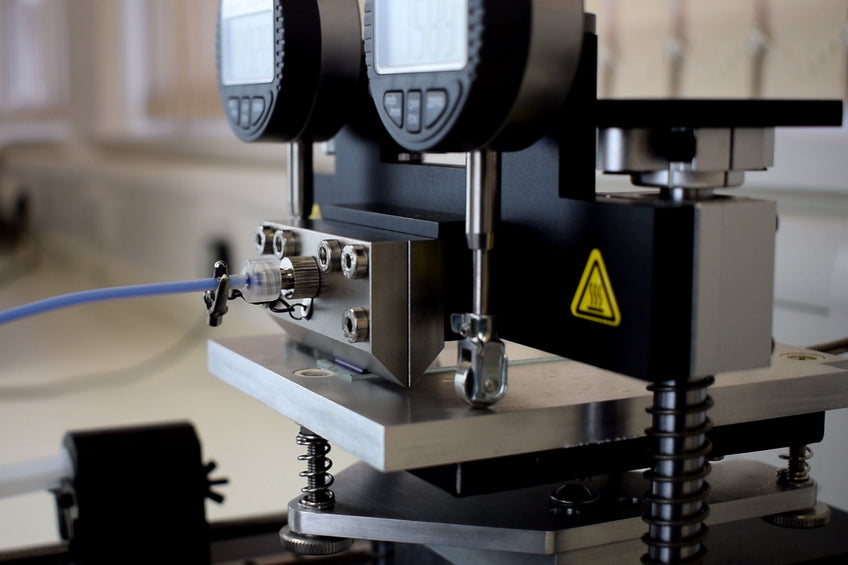
Longer Stage Travel Length
The stage travel length has also been extended, from a maximum of 100 mm to 150 mm. This allows the slot die coater to accommodate larger substrates and allows for coating multiple substrates in a single run, thereby improving efficiency and throughput. Therefore, this improved slot die coater design supports more diverse applications, such as enabling the deposition of coatings over a wider area without repositioning, suitable for applications ranging from research and development to large-scale production.
Expanded Coating Width
One of the significant advancements in our latest slot die coater model is the expanded coating width capability of the slot die head. This enhancement allows for broader coverage and increased efficiency in coating applications.
The maximum coating width has been doubled - increasing it from 50 mm to 100 mm. The wider coating width gives users the ability to coat larger substrates or multiple smaller substrates simultaneously, this can cater to a manufacturer’s diverse needs.
Easier Use with Two-Point Stage Levelling Mechanism
Among the array of upgrades in our latest slot die coater model, we have redesigned it's stage levelling mechanism. This improvement not only ensures better substrate alignment but also enhances the overall precision and consistency of coating applications.
The new levelling mechanism is simpler, using an improved two-point levelling system. It also allows for finer adjustment of the stage due to the customized adjustment screws, and the tensioning mechanism provides higher stability. With this enhancement, there is now an improvement in the accuracy and uniformity of coatings by maintaining precise and consistent substrate positioning and alignment.
New Software Allows Bidirectional Coating
There is also now the integration of bidirectional coating capability, made possible by updated software. This enhancement revolutionizes coating processes by allowing both forward and reverse coating directions. This versatility enables finer control over the deposition of coatings, enhancing precision and efficiency across a wide range of applications. The ability to switch between coating directions seamlessly accommodates varying substrate requirements and coating techniques, ensuring consistent results in diverse manufacturing environments.
Coming Soon: Customizable Add-Ons
We are planning to introduce customizable add ons for the slot die coating system. These will allow it to coat foils and other highly flexible materials for enhanced coating applications. By integrating foil capabilities into our coater, you can explore an additional step on the transition from small scale R&D samples to large scale roll-to-roll processing using the same machine. This simplifies the process by allowing formulations and deposition conditions to be directly translated from rigid small substrates to larger foils, and saves money by allowing this all in one instrument.
As part of our commitment to advancing coating technology, we also plan to integrate a meniscus camera into our slot die coater. This addition aims to revolutionize the coating process by providing real-time visual monitoring of the meniscus formation, enhancing control and precision in coating applications. Planned data integration from the meniscus camera aims to support continuous process improvement, enhancing efficiency and reliability in production.
Slot Die Coater
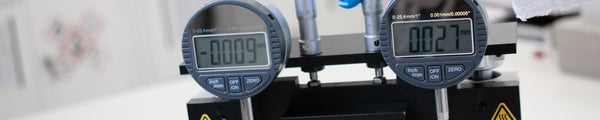