Spin Coater Speed: Key Features
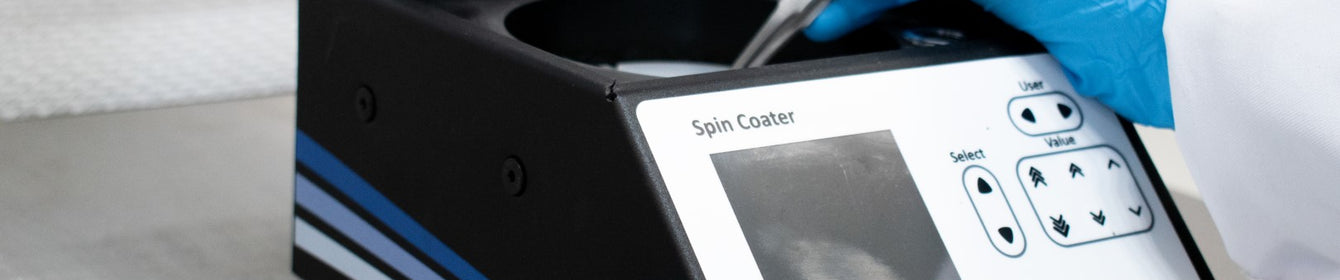
The spin speed features in your spin coater are important as they can characterize and alter the thin films you produce. The Ossila Spin Coater includes several different spin speed features and specifications to offer you optimal levels of control over your final film.
Spin Speed Range
Spin speed range refers to the range of rotational speeds that a spin coater can achieve. It is typically specified in rotations per minute (RPM). The RPM setting determines the speed at which the substrate or sample rotates during the spin coating process.
Higher RPM values typically result in thinner coatings, while lower RPM values lead to thicker coatings. By adjusting the RPM, you can control the desired thickness of the coating layer. Spin speed also has an effect on solvent evaporation. Higher RPM values can promote faster solvent evaporation during the spin coating process.
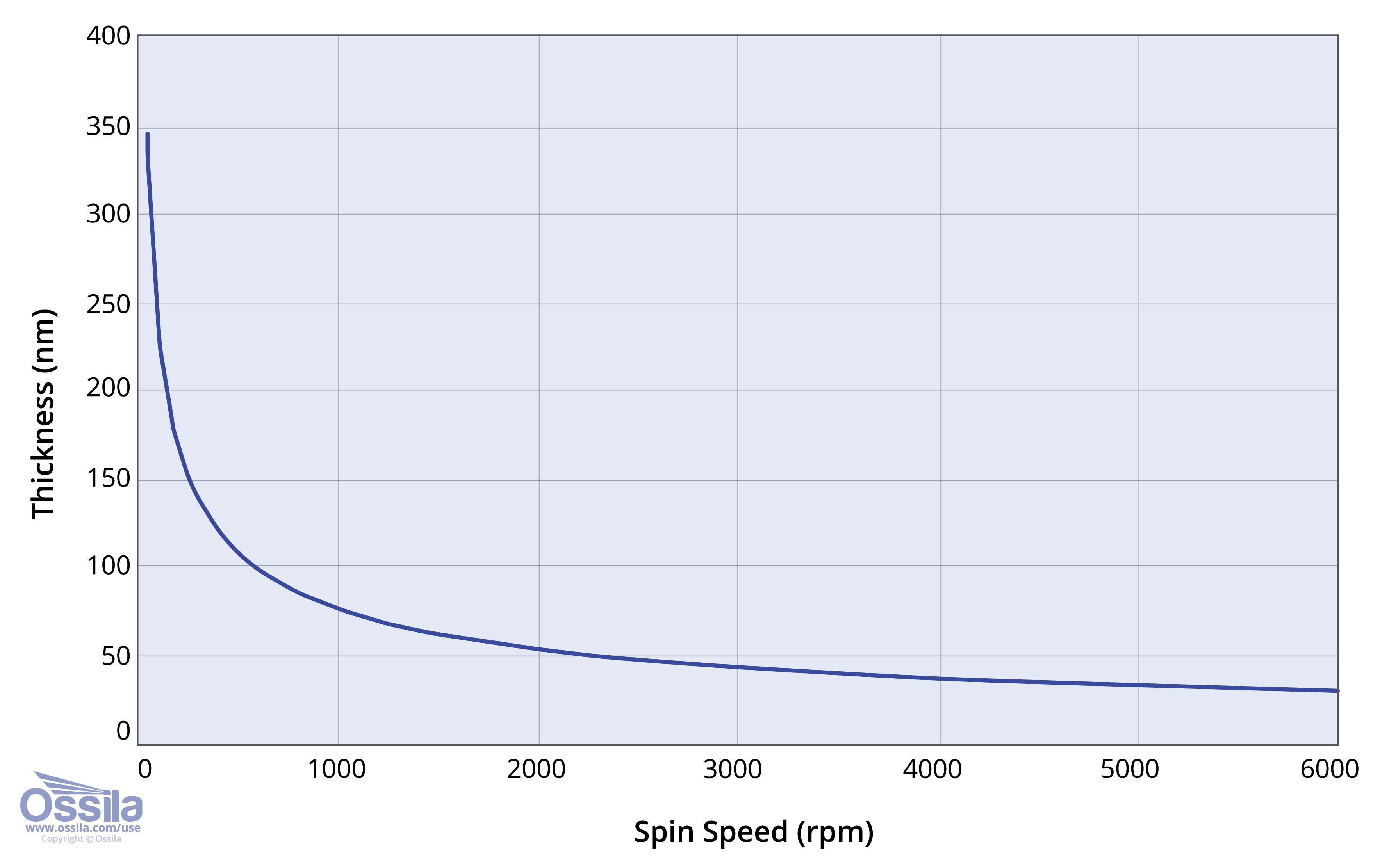
RPM is also useful in coating homogeneity, playing a role in achieving more uniform coating deposition. The centrifugal force generated spreads the material evenly across the substrate, reducing the chances of uneven coating thickness. Optimising the RPM for a specific coating solution and substrate size can improve coating uniformity and minimise defects.
Optimized RPM can also be used to minimize edge effects, which cause variations in coating thickness near the edges of the substrate. With higher RPM values, the liquid tends to migrate towards the edge, and excess materials can be expelled from the substrate entirely due to the centrifugal force, reducing the accumulation of material on the substrate. This can help to mitigate edge build up and promote a more uniform coating thickness across the substrate.
While the RPM can improve your coatings, it can also present some challenges if not correctly controlled. The formation of macroscopic defects such as rings or non-uniform regions in the coating can be influence by the spin speed. With excessively high RPM values, the centrifugal force can cause the coating material to flow away from centre, forming centrifugal rings. Conversely, if the RPM value is too low then the coating may not spread adequately and result in patchy or uneven coatings.
Selecting an appropriate spin speed can aid in preventing these defects and enhance film quality.
Spin Speed Accuracy
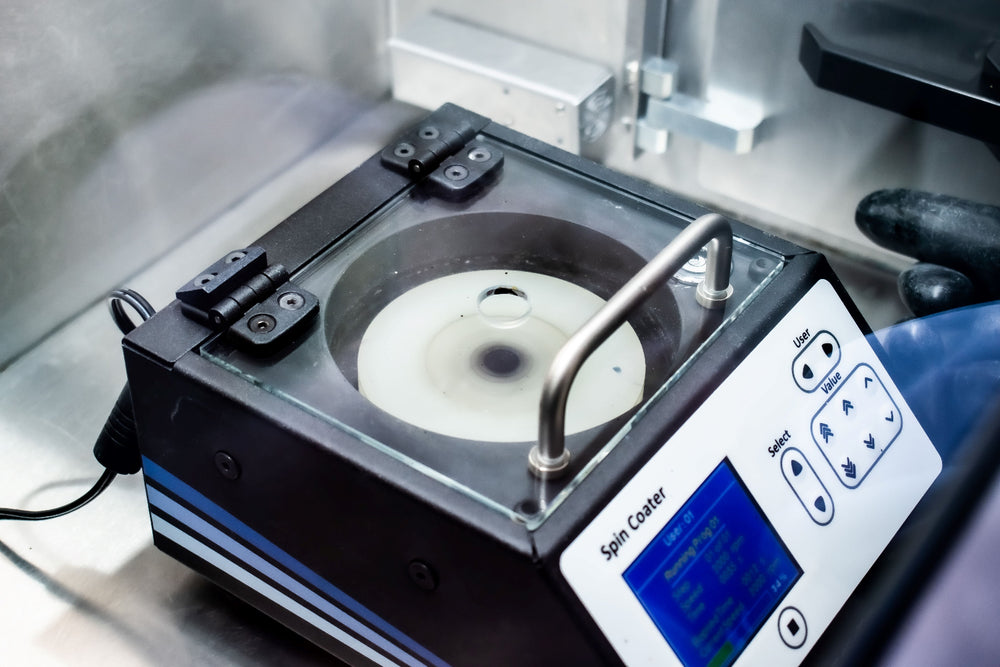
Another important specification in a spin coater is spin speed accuracy. The accuracy directly impacts the control and consistency of the coating process.
Spin speed accuracy means that the spin coater can consistently achieve the desired rotational speed for each coating process. This is particularly crucial in processes where the coating thickness, morphology, or other characteristics need to be precisely controlled.
A high spin speed accuracy grants better reproducibility between different coating runs, reducing variations, and improving the overall reliability of the process. It enables researchers to study the effect of a slightly different spin speed on the resulting film characteristics. A spin coater with high speed accuracy can minimise variations and increase coating uniformity.
In certain applications, such as thin film electronics, the performance of the coating can be directly influenced by the speed accuracy. Factors like thin film morphology variations, layer thickness, and crystallinity can be manipulated.
Spin Speed Acceleration
Acceleration may not always be necessary within your coatings, but it can provide several important benefits. It helps to ensure a uniform distribution of material across the substrate.
As the spin coater starts at a lower speed and gradually accelerates, the risk of an uneven or patchy coating is reduced. In addition to this, acceleration can also play a crucial role in achieving a precise final coating thickness. You can optimise the amount of material that is spun off the edges and ensure an accurate coating thickness across the entire substrate.
By maintaining consistency in the acceleration profile, you can ensure that the coating process is consistent across multiple samples or batches, leading to reliable and repeatable results. Specific acceleration profile and requirements may vary depending on the coating material, substrate, and spin coater used. Optimal acceleration settings need to be determined through experimentation and optimisation for each specific application.
Programmability and Control

Programmable settings and advanced speed control options are available in some models, including the Ossila Spin Coater.
Programmability allows users to define and save customised spin profiles, these specify the desired spin speed, acceleration, deceleration, and duration for each stage of the coating process. This capability enables you to fine-tune the coating parameters for different materials, substrates, or coating applications.
With programmability, the spin coater can consistently reproduce the same spin profiles for multiple coating runs. This ensures repeatability of the coating results, reducing variations and improving overall process control. Users can achieve more consistent coating quality and reduce the potential for human error.
Some coatings require multi-step or intricate processes, such as ramp-up and cooldown stages, multiple spin cycles, or alternating spin directions. Programmability allows for the automation of these complex processes, eliminating the need for manual intervention.
By using multi-step speed control with varying speeds, the formation of edge beads is minimized, improving the overall coating quality. Furthermore, different materials and coating solutions may require different spin speeds to achieve the desired coating thickness. With multi-step speed control, you can set different speeds for various stages of the coating process, ensuring uniform distribution and thickness of each deposited layer.