Lithium-Ion Battery Components and Working Principle
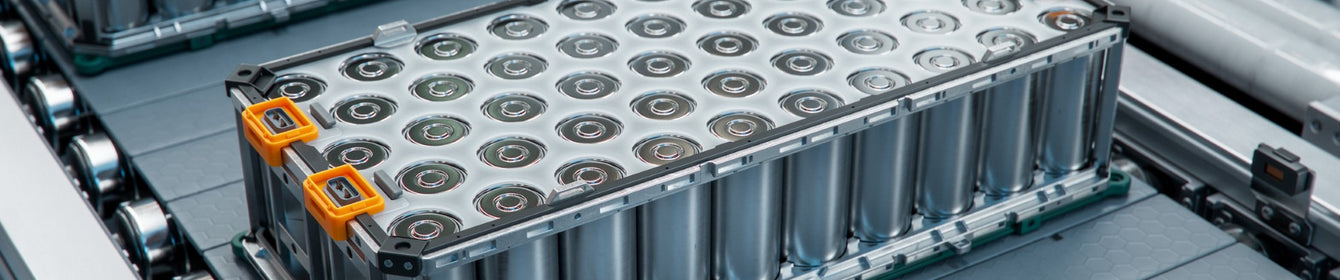
Lithium-ion batteries operate based on electrochemical reactions, specifically redox reactions involving lithium and sometimes other redox-active elements. These reactions result in the movement of lithium ions between the electrodes and the flow of electrons through an external circuit. During operation, lithium ions intercalate into the electrode materials, depending on whether the battery is charging or discharging. Intercalation refers to the insertion of lithium ions into the crystal or molecular structure of the electrode material. It is essential that the electrode materials can host lithium ions without significant changes in structure or volume to ensure the battery remains safe and efficient.
Lithium-Ion Battery Components
A lithium-ion battery has several important components that enable lithium ions to flow through the system. Lithium-rich cathode active materials, such as such as lithium iron phosphate and lithium cobalt oxide, supply the lithium ions. Anode active materials typically have a low voltage (electrochemical potential vs Li/Li+) and high capacity. A non-conductive electrolyte and separator prevent short circuits by keeping the electrodes electrically isolated. Electrons released by lithium during oxidation at the electrodes are collected by the current collectors and transported through an external circuit. These materials also enable lithium-ion transfer while keeping the electrons confined to the external circuit or their respective electrodes.
A lithium-ion battery cell consists of five components:
Lithium-ion Battery Component | Description | Example |
---|---|---|
Cathode | High voltage and high capacity | Lithium Iron Phosphate Powder |
Anode | Low voltage and high capacity | Graphite Powder |
Electrolyte | Solvent electrolyte with lithium salt | Ethylene Carbonate, LiPF6 |
Separator | Porous polymer that moderates the ion flow and separates the anode and cathode | Polyethylene |
Current collectors | Support the electrode materials and ensure electrons travel to external circuit | Copper foil |
How do Lithium-Ion Batteries Work?
Lithium-ion batteries work via electrochemical reactions. By applying a voltage to a battery, the lithium ions are driven through the electrolyte to intercalate into the anode material. The low electrochemical potential of the anode draws lithium ions to it, making it the site of lithium-ion reduction.
Lithium Electrochemical Reactions
Oxidation: Li → Li+ + e-
Reduction: Li+ + e- → Li
The oxidation of lithium provides access to electrons that can be used to power a device as part of the external circuit. Conversely, the reduction of lithium ions during charging enables energy to be stored at the anode. Other redox-active metals, such as nickel and cobalt, within cathode materials may also undergo redox reactions. Nickel, in particular, can participate in multi-electron redox processes, which contributes to increased energy capacity in the battery.
When rechargeable batteries are assembled, they are in a discharged state. Lithium-ion batteries are charged by connecting them to a power supply. The applied voltage causes the lithium ions intercalated within the cathode to move towards the anode.
Charging Lithium-ion Batteries
During charging, lithium ions flow away from the cathode to the anode due to a potential difference between the two electrodes. Li+ ions are driven through the electrolyte to the anode where the electrons are accumulating, via an external circuit.
The simultaneous accumulation of Li+ ions and electrons at the anode enables charge storage. Upon intercalation into the anode material (typically graphite), the lithium ions are reduced back to neutral lithium atoms. Electrons that have accumulated at the anode via the external circuit enable to reduction to take place.
Discharging Lithium-ion Batteries
The charged lithium-ion battery is used to power a circuit which results in the battery discharging. When discharging, electrons flow from the anode through a circuit, providing electrical power to the device, and return to the cathode.
At the same time, lithium undergoes oxidation at the anode and lithium ions flow back to the cathode material, through the electrolyte. Once all the lithium ions are intercalated with the cathode, the battery requires charging to be used again.
Lithium-Ion Battery Materials and Properties
The materials used in lithium-ion batteries are important because they can alter the specific energy, specific power, cycle life, and the safety of the battery.
Cathode Materials
Battery research has focused largely on the cathode material as it is the most limiting of the four main components. In typical lithium-ion batteries, the cathode plays a vital role in supplying the ions. Therefore, research is essential to determine the best morphology and chemistry for each specific battery application.
The choice of materials is crucial as the properties depend on the elements and morphology of the cathode. The morphology of the cathode affects how fast the ions can diffuse through its own structure. If the integrity of the morphology is not stable enough, there will be a limit on the number of cycles the electrode can take before degrading to an unusable state. The chemistry of the cathode determines how many lithium ions are available for intercalation.
The most common cathode materials include:
Browse more cathode active materials
Anode Materials
The anode must supply a large discharge voltage while remaining isometric. Graphite is commonly used. It has a large discharge profile and porous nature which allows lithium ions to interlap with the structure during charging and vice versa.
The most common anode materials currently feature graphite or hard carbon, but research is testing new anode materials. They offer a higher charge capacity but tend to expand or contract during charging.
Common anode materials include:
Electrolytes
The electrolyte carries lithium ions from the cathode to the anode, and vice versa, without allowing a flow of electrons. It is important to consider the chemical and physical reactions that could occur between the electrolyte and other battery components. The electrolyte must be chosen carefully to prevent voltage induced electrochemical decomposition or rapid oxidation.
Generally, electrolytes are a mix of electrolyte salts in either an organic or inorganic solvent. Electrolytes are also available in either an aqueous or solid solution, although solid electrolytes are a fairly new research area. Solid state electrolytes are emerging as a new substitute for aqueous solutions. They have a higher energy density and improved safety, through a larger range of operating temperatures and dendrite prevention.
Separator
The separator material provides structural integrity and acts as an inbuilt safety feature to moderate ion travel. If ions move through the electrolyte too fast there is potential for thermal runaway, so the separator is designed to close or open their pores depending on temperature.
An interesting area of research is the design of separators to help prevent dendrite and solid electrolyte interphase formation. This prolongs the battery lifetime. An uneven distribution of lithium ions moving through the separators can cause a spike like formation, creating a risk of penetration and short circuiting. By maintaining a uniform ion distribution, the dendrite growth can remain evenly distributed to prolong the life of the battery.
Explore the range of high-purity cathode materials designed for high-capacity, high-voltage batteries to maximize energy density.
Learn More
Lithium-ion (Li-ion) batteries can catch fire due to a process known as thermal runaway, which is triggered by various factors and involves a series of heat-releasing reactions. While Li-ion batteries are widely used in laptops, cameras, and electric vehicles (EVs) such as scooters and cars, their rise in popularity has not been without issues. In the UK alone, fire services responded to 921 lithium-ion battery fires in 2023, a 46% increase from the previous year.
Learn more...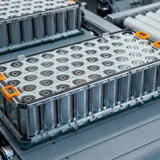
Lithium-ion (Li-ion) batteries, developed in 1976, have become the most commonly used type of battery. They are used to power devices from phones and laptops to electric vehicles and solar energy storage systems.
Read more...Contributing Authors
Written by
Scientific Writer
Edited by
Application Scientist
Diagrams by
Graphic Designer