Customer Case Study: Power Roll
Complementary suite of materials and equipment enables Power Roll to quickly take prototypes from lab-scale to large-scale
Challenges faced by Power Roll |
---|
|
Power Roll is an award-winning startup aiming to commercialise its innovative solar photovoltaic energy generation and storage technologies. They were challenged by the large amounts of time, money, and maintenance associated with the various processing equipment needed for their solar cell research.
More often than not, these pieces of equipment would also come with features that were unnecessary and irrelevant for Power Roll's specific research needs. This translated to steep learning curves and lengthy process optimisation periods, as there was a lack of technical resources and user support guides for the particular methodology processes they needed to use.
Solutions provided by Ossila |
---|
|
Wanting to simultaneously accelerate their research and stay within budget, Power Roll chose Ossila's Spin Coater as an affordable, compact, and vacuum-free alternative to the traditional spin coater they already owned. Because it does not require a vacuum line, there was a reduced need for servicing and maintenance, therefore lowering costs and downtime.
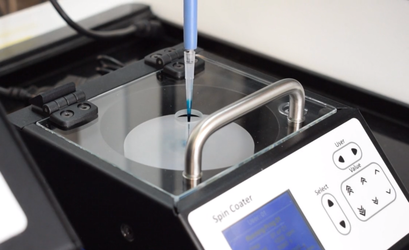
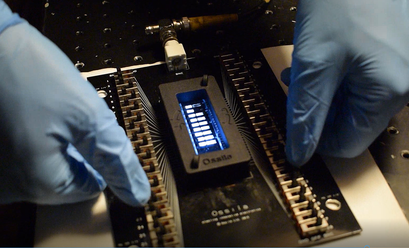
To efficiently optimise small-scale fabrication with reliable baselines before transferring that knowledge onto their own patented PV architecture, Power Roll use Ossila's ITO PV substrate (8-pixel) and Measurement Aperture Mask (8-pixel) with the I-V Curve Measurement System to characterise completed photovoltaic cells.
When they were satisfied with the results of their small-scale fabrication and prepared to scale up, Power Roll used the Ossila Slot Die Coater. The slot die coater's compact size meant that it could easily fit within a glove box and fumehood in their small labs. Its easy-to-use integrated digital control system (in combination with the online guides on the Ossila website) also meant that the barrier-to-entry was lowered for their researchers, and they could start coating after a short training period.
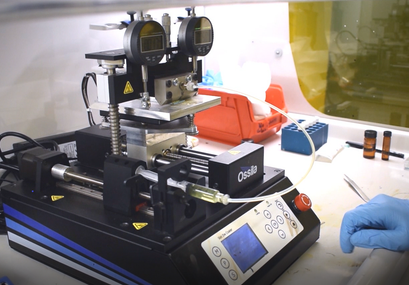
Results |
|
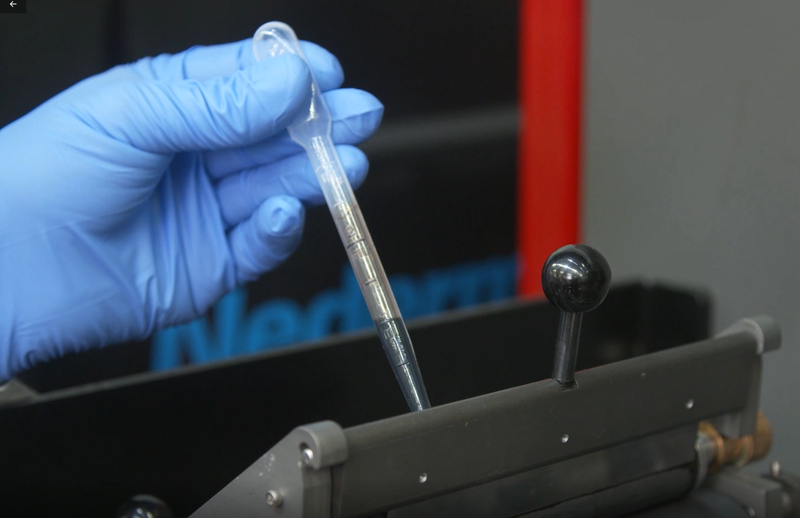
"We find Ossila's equipment very user-friendly and practical for our processes (solar cell research), and have used them since 2015. They provide good value for startups and SMEs, especially the consumables and equipment which are part of the Ossila Solar Cell Prototyping Platform."
- Dr. Trevor McArdle, Senior Research Scientist at Power Roll
As a result, vast amounts of time have been saved during their lab-scale optimisation process. In their labs, Power Roll see repeatability and efficiency improvements in a range of daily tasks - including substrate cleaning, material screening, and device testing. Establishing a reliable baseline is hassle-free and straightforward - freeing up their time to focus on optimising key variables.
Their throughput of day-to-day device fabrication has greatly increased thanks to a combination of substrates, materials, processing equipment and test equipment from Ossila - all designed to work coherently together.
Want to be featured here?
If you are an Ossila customer and want to share your experiences of how our materials and equipment have helped you in your research, then we would love to hear from you! Please contact us and mention "Customer Case Study Feature Submission" in your message.