Spin Coater Advanced: Upgrades and Specifications
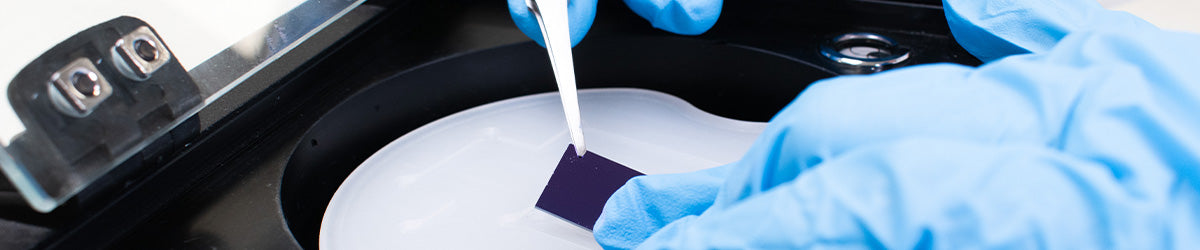
The advanced model of the Ossila Spin Coater offers more control than the classic spin coater in a wide range of areas including:
- enhanced user profile capacity
- improved speed stability and range
- extended spin times
- higher chemical and thermal resistance
These advancements make the advanced spin coater ideal for high-precision and demanding applications, providing greater versatility, durability, and efficiency.
Increased Stability and Precision
The new and updated spin coater offers superior speed stability with an error margin of less than 0.25%, significantly lower than the <2% error of our standard spin coater. This ensures more consistent and reliable coating processes. Speed stability is a critical factor in spin coating, as it directly impacts the uniformity and quality of the coated layers.
Inconsistent speeds can lead to variations in the thickness and properties of the coating. High-precision applications benefit greatly from this enhanced stability, as it minimises the risk of variations in coating thickness and quality. In fields such as nanotechnology and advanced materials science, even minor variations in coating can significantly impact the performance and characteristics of the final product.
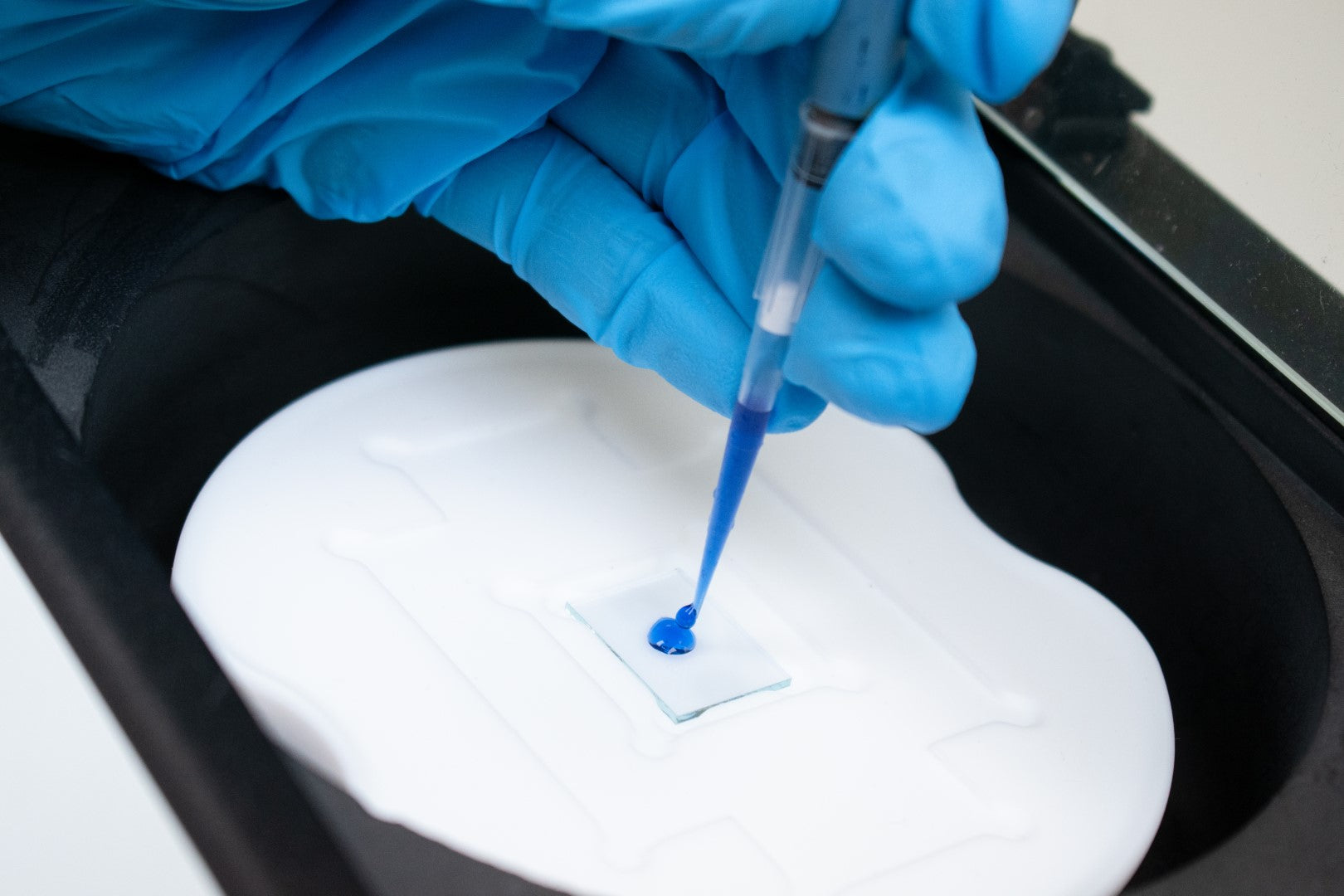
Faster Speed Range
The new model also has an increased speed range from 500 – 10,000 RPM (compared to the classic spin coater with 120 – 6,000 RPM).
This will allow users finer control over the coating process. Choosing the right spin coater speed is crucial for determining the versatility and applicability of the device across different coating processes. A broader speed range means you can tailor your spin speed to your specific needs, accommodating a wider range of materials and desired coating thicknesses.
The ability to reach up to 10,000 RPM allows for the creation of ultra-thin films, essential in industries such as electronics and optics where thin, uniform layers are crucial. Also, with a higher maximum speed, it means the new Ossila spin coater can handle a wide variety of materials, including those with higher viscosities that require more force to spread evenly.
In fields where precise control over film thickness is paramount, the Ossila high speed spin coater’s ability to operate at up to 10,000 RPM ensures very thin, highly uniform coatings. This is a crucial parameter in the production of microchips and other nanoscale devices.
Longer Spin Cycles
With the high-speed spin coater, the maximum speed has been extended from 1000 seconds to 3600 seconds. Spin time is a key parameter in spin coating, determining how long the substrate is subjected to rotational forces to achieve the desired coating thickness and uniformity.
Longer spin times can be necessary for specific applications, allowing for better solvent evaporation and more controlled layer formation. In the development of advanced materials, such as multilayer coatings or films with graded properties, longer spin times can be crucial.
The advanced spin coater’s extended deposition time allows for these complex processes to be executed effectively. This is also a useful feature in biotechnology applications, this is where coatings on substrates may require slow evaporation to ensure biocompatibility or the integrity of biological molecules, the ability to extend spin time up to an hour is particularly beneficial.
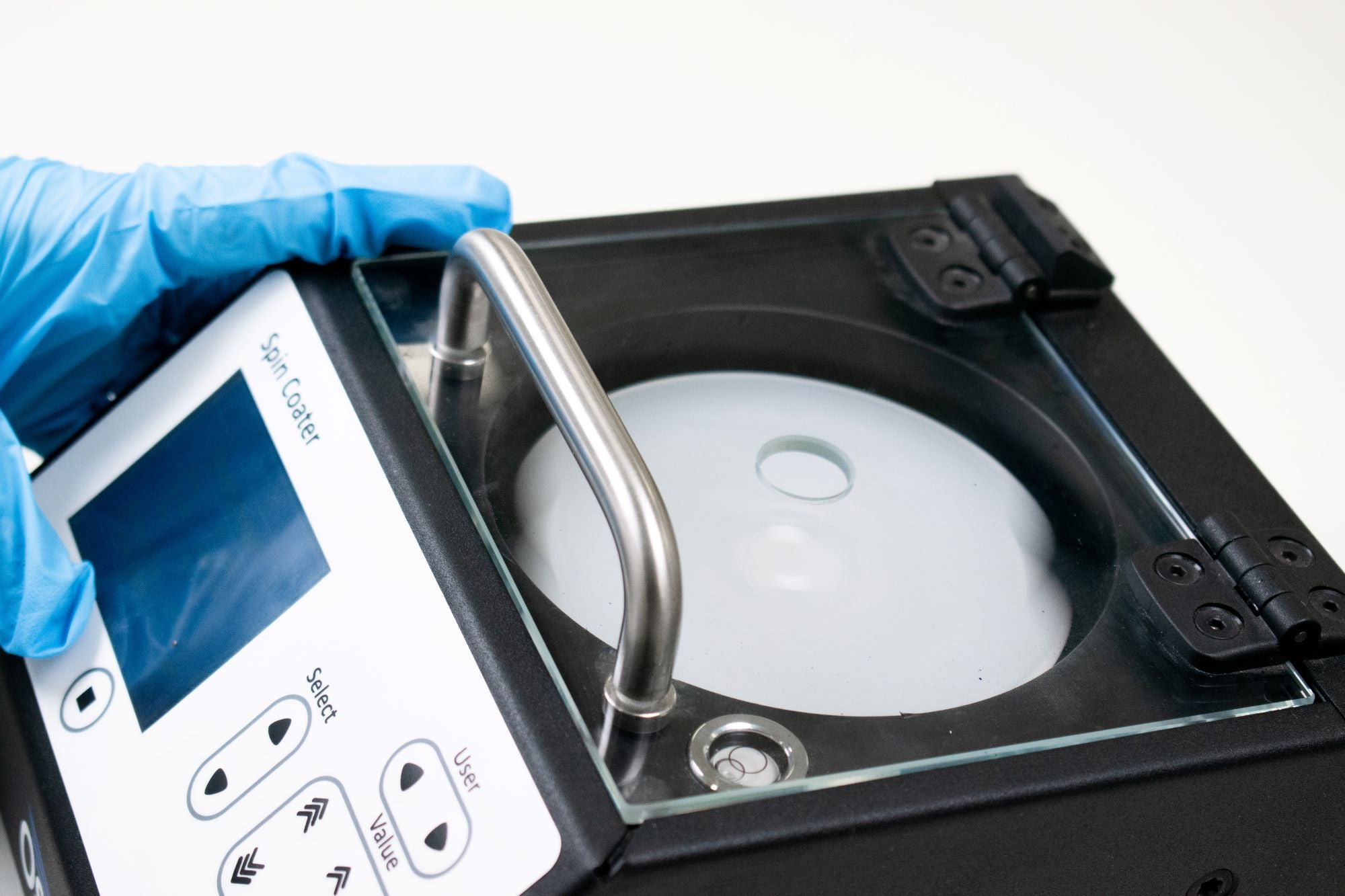
Material and Build Durability
The spin coater advanced upgrades the bowl material from polypropylene to PTFE, known for its enhanced chemical resistance and durability. High quality materials ensure that the device can withstand rigorous use and exposure to various chemicals without compromising its structural integrity or functionality.
The upgrade to a PTFE bowl offers superior chemical resistance compared to polypropylene. It is non-reactive with many chemicals, making it ideal for use with a wide range of solvents and coatings. PTFE’s non-stick properties also make the bowl easier to clean, reducing the risk of cross-contamination between different coating processes and simplifying maintenance routines. Further reinforcement has been made through the upgrade from steel casing to powder coated steel.
While slightly heavier at 3.7 kg, the increased weight reflects the sturdier build and enhanced durability of the Spin Coater Advanced.
New Spin Coater Chuck Design
We have also completely redesigned our spin coater chuck to improve efficiency and performance. Key enhancements include better aerodynamic and mechanical design, resulting in higher speeds, reduced vibrations, and improved airflow.
The new chuck supports multiple substrate sizes, allowing for versatile use without changing chucks. Further innovations aim to deflect solvent vapors, minimize stagnant air pockets, and optimize airflow uniformity. Mechanically, the chuck is lighter yet more stable, with increased mass towards the center to reduce inertia, enabling higher speeds and better energy efficiency. These improvements enhance the overall performance and longevity of the spin coater system.
Spin Coater
