Syringe Pump Fluctuations
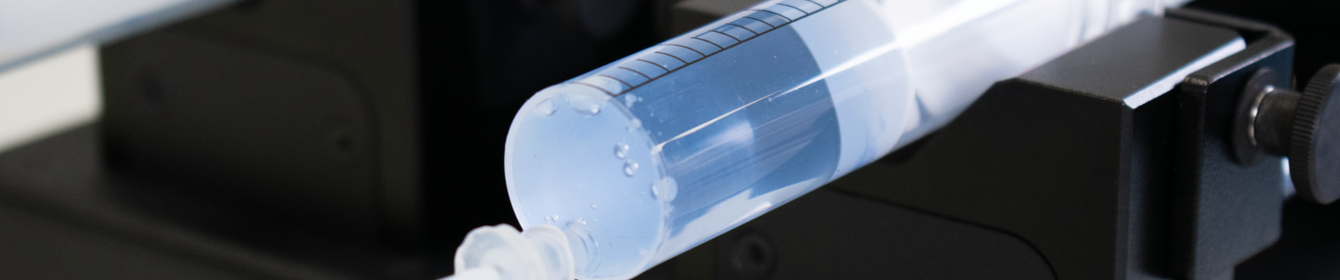
Fluctuations in laboratory syringe pumps can refer to variations or inconsistencies in the flow rate or volume delivery of the pump. Fluctuations in research syringe pumps are mostly encountered in the fluctuation of flow rates. The syringe pump is ultimately designed to deliver precise volumes of fluids at controlled rates, but several factors can cause fluctuation in flow rate such as:
- Variations in viscosity of the fluid being pumped
- Air bubbles in the system
- Temperature changes
- Mechanical wear and tear
The Ossila Syringe Pump minimizes fluctuations by using microstep technology and high precision motors.
Flow Rate Fluctuations in Microfluidics
These fluctuations can have a serious implication in microfluidic applications such as droplet microfluidics. Flow rate fluctuations have been shown to increase polydispersity . Polydispersity refers to the distribution of particle sizes or droplet sizes within a sample, and it is a critical parameter in many microfluidic processes.
Fluctuations in flow rates can result in non-uniform shear rates across the fluid stream. Shear forces play a crucial role in controlling the size and uniformity of particles or droplets generated in microfluidic processes. Variations in sheer rates can lead to inconsistent breakup or coalescence events, resulting in a broader distribution of sizes.
Fluctuations in flow rates can induce instabilities in fluid flow, such as Taylor dispersion or Rayleigh-Plateau instability. The Taylor dispersion refers to the spreading out of solute molecules or particles in a flowing fluid due to the combined effects of advection and diffusion. The Rayleigh-Plateau instability describes the spontaneous breakup of a cylindrical liquid column into a series of smaller droplets due to capillary forces. These instabilities can cause irregularities in the breakup or coalescence process, leading to the formation of particles or droplets with diverse sizes and shapes.
Volume Errors Due To Fluctuations
Fluctuations in syringe pumps can also directly contribute to dispense volume error. This is when the volume of solution deposited deviates from the intended volume of fluid dispensed. These errors can arise from mechanical inaccuracies such as irregularities in the syringe barrel or plunger, flow rate variability due to inconsistent pump speeds, and pressure fluctuations within the syringe. Additionally, temperature changes can affect the fluid's viscosity and the syringe's material, leading to volume discrepancies. Furthermore - operator errors, such as improper setup or misinterpretation of instructions, further contribute to volume errors. To mitigate these issues, it is essential to regularly maintain and calibrate the syringe pump, use high-quality syringes, implement consistent operating conditions, and conduct routine performance checks to ensure accurate and reliable dispensing.
Causes of Syringe Pump Fluctuation
Air Bubbles
One of the factors which can cause fluctuations in syringe pumps are air bubbles. These disrupt the flow path and cause irregularities in pumping. When present in the syringe or tubing, air bubbles can compress under pressure, resulting in inconsistent movement of the plunger and irregular flow of the fluid. To overcome this issue, several strategies can be employed.
- Proper priming of the system before operation helps expel air from the syringe and tubing, ensuring continuous fluid flow.
- Using degassed fluids and high-quality syringes reduces the likelihood of air bubble formation.
- Installing bubble traps or air venting devices along the fluid pathway can capture and remove any air bubbles that may form during pumping.
- Regular maintenance, including inspection and cleaning of pump components, ensures optimal performance and minimises the risk of air bubble-related fluctuations.
By implementing these measures, syringe pump operators can maintain smooth and consistent fluid delivery, mitigating the impact of air bubbles on pump performance.
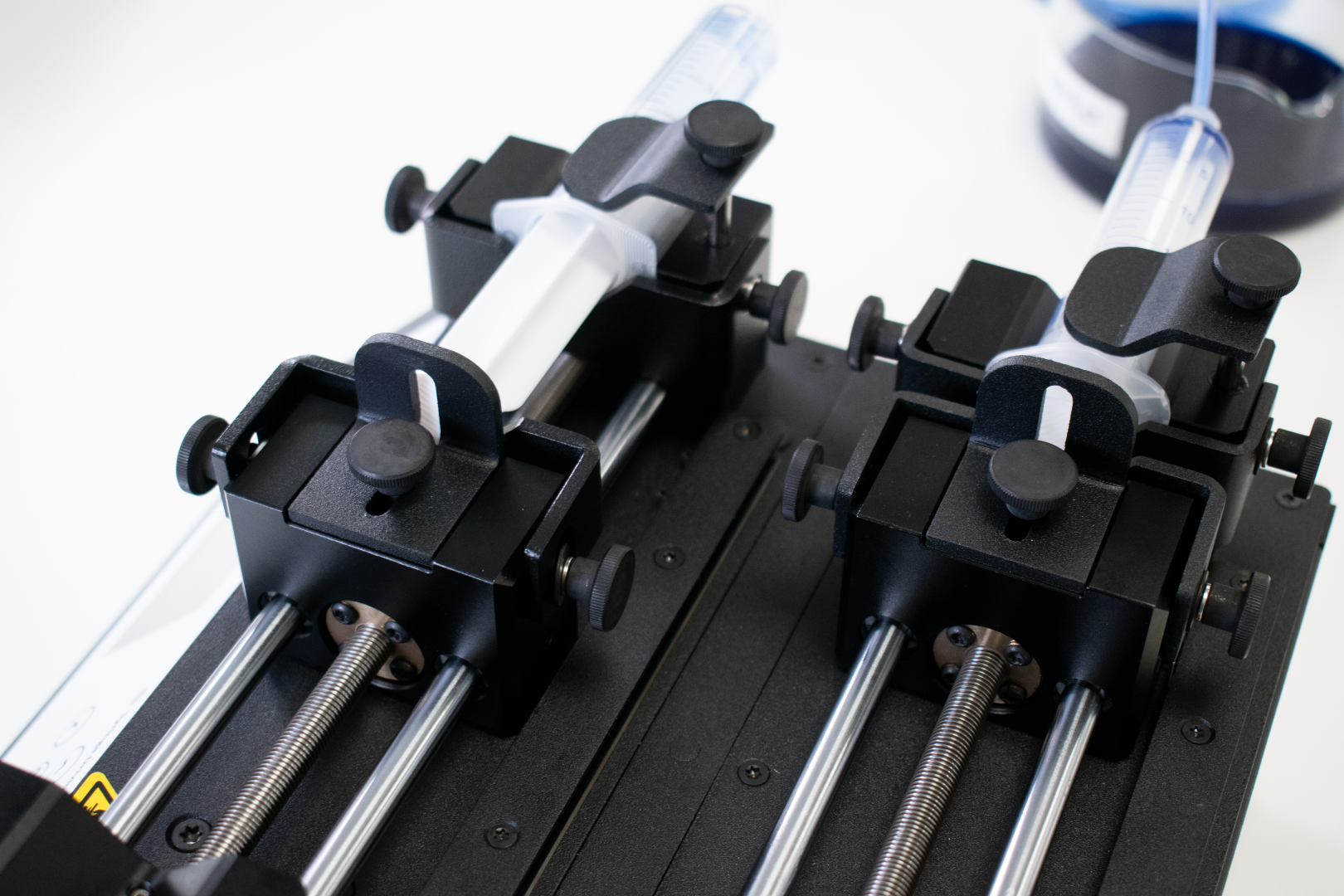
Syringe Driver Fluctuation
A syringe driver fluctuation refers to variations or inconsistencies in the performance of a syringe driver, which can affect the accuracy and precision of fluid delivery. These fluctuations can impact the volume and flow rate of the solution being dispensed, leading to potential errors in applications where precise dosing is critical.
Regular calibration and strict maintenance routines are essential to keep the equipment functioning accurately. Standardising the use of syringe drivers from the same manufacturer and model helps minimise variability. Maintaining stable environmental conditions, such as temperature and humidity, further reduces performance inconsistencies.
Syringe Barrel Variation
Syringe barrel variation refers to inconsistencies or irregularities in the dimensions, materials, or performance of the syringe barrel, which can impact the accuracy and reliability of fluid delivery. These variations can affect the volume measurements and the flow characteristics of the syringe, leading to potential errors in dispensing applications where precise dosing is essential.
Overcoming syringe barrel variations involves implementing precise and methodical approaches to ensure the consistency, accuracy, and reliability of experimental results. One fundamental strategy is the standardisation of syringes used in experiments. Researchers should select and consistently use syringes from the same manufacturer and with the same specifications to minimise variability. This standardisation helps in maintaining uniform experimental conditions, thus improving the reproducibility of results.
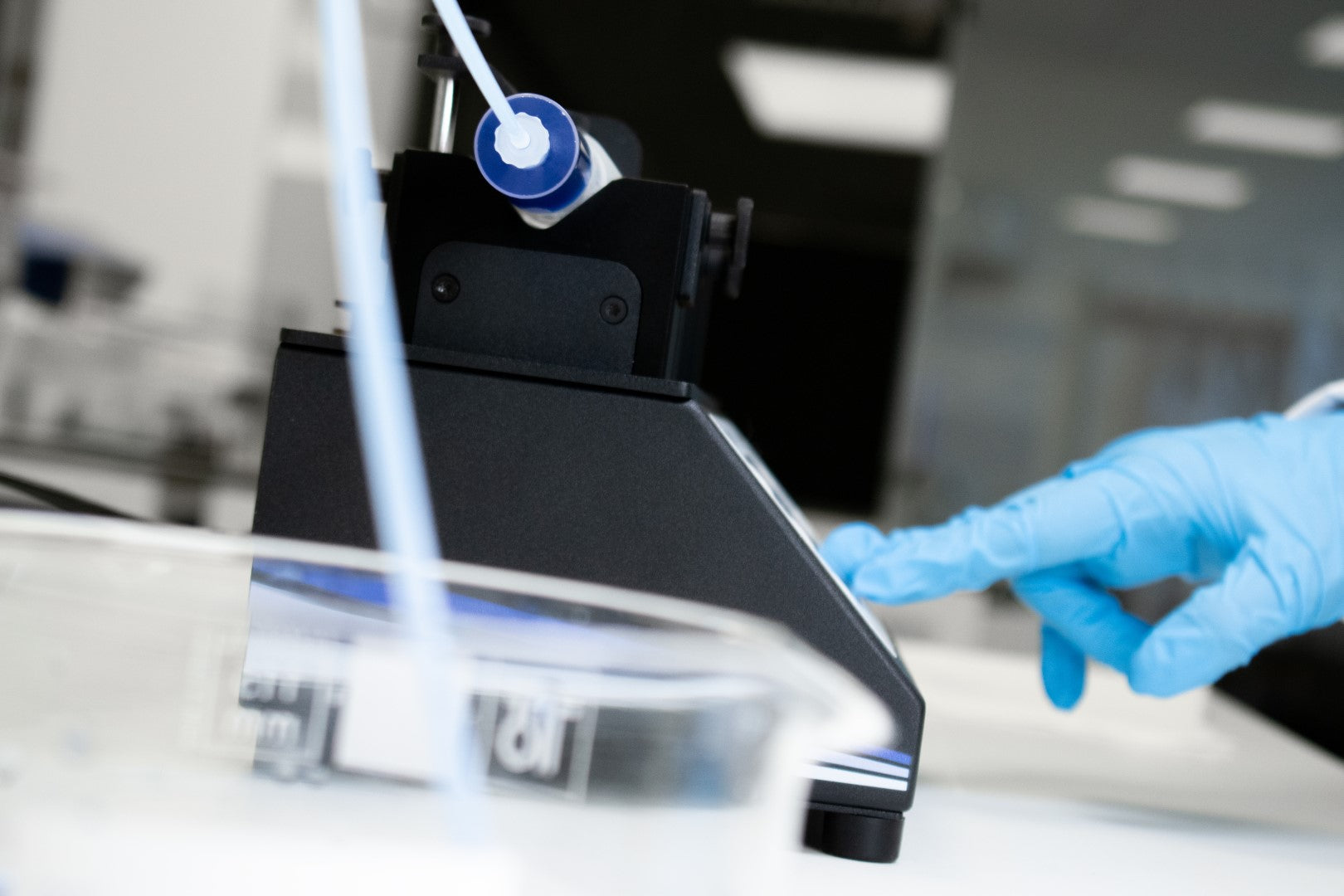
Fluctuations in Ossila Syringe Pump
Overall, monitoring fluctuations in syringe pumps is essential for maintaining the accuracy and reliability of experimental procedures in scientific research. At Ossila, we understand the critical role that precision and reliability play in your research endeavours. That's why our range of syringe pumps is meticulously designed to meet the highest standards of performance and accuracy.
With advanced monitoring capabilities, our syringe pumps empower researchers to maintain tight control over fluid delivery, ensuring the integrity of dosage in a variety of applications, from drug delivery to materials synthesis. Trust our syringe pump design to safeguard the integrity of your research by maintaining tight control over fluctuations in fluid delivery, empowering you to achieve consistent and reliable outcomes with every experiment.
Syringe Pump
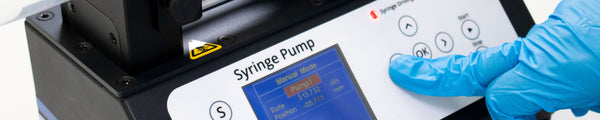
Learn More
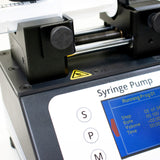
The flow rate for a syringe pump refers to the rate at which a fluid is dispensed or withdrawn from a syringe using a syringe pump. It is typically measured in volume per unit of time. Flow rate is controlled by the syringe pump and can be adjusted based on the requirements of the experiment or application.
Learn more...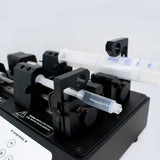
With no external dependencies, both the Ossila Single Syringe Pump and Ossila Dual Syringe Pump are quick and easy to set up and use
Read more...References
- Syringe-pump-induced fluctuation in all-aqueous microfluidic system implications for..., Z. Li et al, Lab on a Chip (2014)